Cogeneration Plant
UConn’s energy requirements are growing as the University continues to construct a number of new buildings as part of its UConn 2000, 21st Century UConn and Next Generation projects.
UConn’s state-of-the-art Co-generation Facility began operation March 15, 2006, replacing several oil-fired utility boilers and enabling the University to meet its own energy needs at the main campus.
Cogeneration is defined as the sequential production of both electrical or mechanical energy and useful thermal energy from a single energy source.
This allows over 80% of the fuel energy to be harnessed, versus 33% from a conventional electric power plant.
Husky Power Meets Storrs Campus Energy Requirements
Electric Capacity: 24.9 Megawatts/Hour
Steam Capacity: 600,000 Pounds/Hour
Chilled Water Capacity: 10,300 Tons/Hour
Contact Us
Associate Vice President, Facilities Operations
Stanley L. Nolan
(860) 486-3208
stanley.nolan@uconn.edu
Associate Director of Utilities Operations
Tim Grady
(860) 486-5567
tim.grady@uconn.edu
Supervisor, Central Utility Plant & Cogeneration Facility
Tim Bilyeu
(860) 486-5548
timothy.bilyeu@uconn.edu
May 2022 Outage
During May each year the Husky Power Team takes the Cogeneration Facility off line for maintenance. This maintenance is performed to ensure the Facility continues to operate with high reliability in the most efficient manner. The PowerPoint link below is the May 2022 outage. Many thanks to the dedicated staff and contractors who support this work every year.
Special recognition to Edward Ramos Riguard, our student intern, for the media concepts
The Cogeneration facility provides a two-fold reduction in emissions:
1. Natural gas, a cleaner burning fuel, is used by the facility to generate electricity and steam for heating and evaporative cooling.
2. Steam production in the process removes the need to construct separate steam-production facilities that would burn their own fuel and have their own emissions.
Most power plants on the electric grid are considerably less efficient than co-generation facilities because they do not capture and utilize the steam for heating and cooling. Also, “distributed generation”, like UConn’s Central Utility Plant, prevents the efficiency loss and congestion that occurs during transmission and distribution of electricity from the point of generation to distant electricity customers.
More about UConn’s Cogeneration Plant
Positives for our Environment
- The Central Utility Plant meets nearly all of UConn’s projected 2025 energy needs and improves reliability while producing fewer emissions than the older boilers which were replaced. Additionally, the facility decreases UConn’s energy costs over the entire forty-year design life of the plant. The University expects to save nearly $180 million in energy costs during the plant’s life.
- An average U.S. household uses about 11,000 kilowatt-hours (kWh) of electricity each year. The UConn Central Utility Plant replaces about as much electricity as 20,000 households use to the grid for consumer use.
- The UConn Central Utility Plant reduces CO2 (greenhouse gas) emissions by an estimated 30,000 tons each year versus emissions from fossil-fueled power plants serving the regional electric grid.
- The UConn Central Utility Plant is a generator of Class III Renewable Portfolio Standard credits as an efficient combined heat and power plant.
- Twenty-five percent of the Renewable Energy Credits are returned to the Connecticut Clean Energy Fund for state wide energy conservation initiatives.
Electrical Description
The UConn Central Utility Plant uses natural gas, with fuel oil as a back-up fuel source, to fire three Solar Taurus 70 combustion turbine generators to produce electricity. The combustion turbines have a rated thermal efficiency of 34 percent. Waste heat from the turbines is used to produce steam, which is then used in a steam turbine generator to produce additional electricity. Low-pressure steam is distributed for campus use.
Thermal Description
High pressure 600 psig saturated steam from the RenTech Heat Recovery Steam Generators drives a Tuthill-Murray steam turbine or is reduced by Pressure Control Valves. The medium pressure 127 psig steam turbine exhaust or reduced steam is supplied to internal plant use, to provide Chilled Water via the three York centrifugal chillers or to the UConn Campus Distribution network. The network reduces the steam to low pressure 65 psig for building heating and kitchen service.
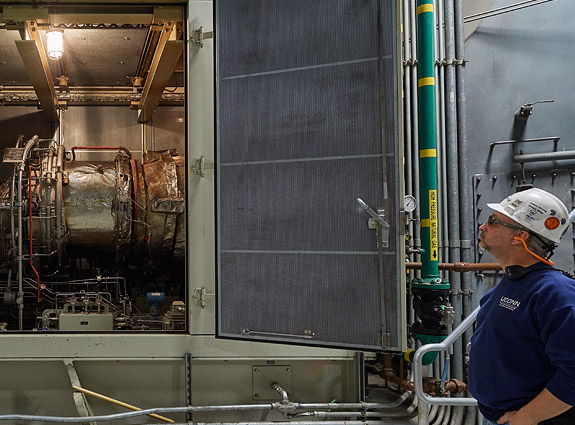